How to Provide and Maintain Safe Work Equipment at School
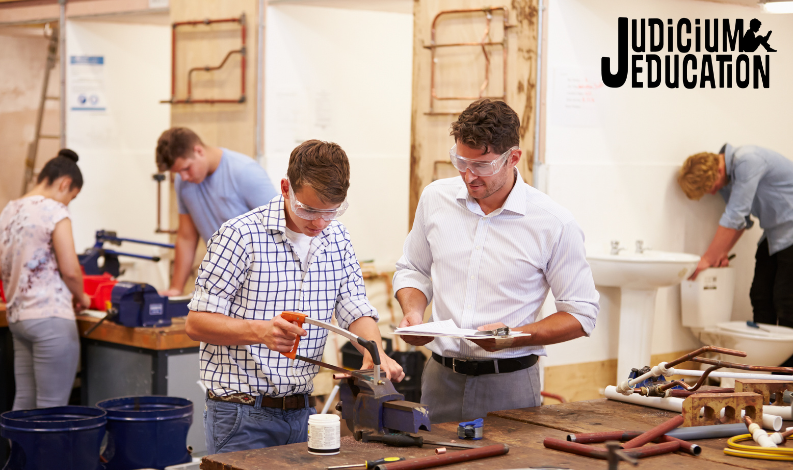
This blog is based on Judicium’s Health and Safety ‘Sofa Session’ from the 22nd of May, with our resident expert Sally O'Donnell. This session focused on a brief overview on the regulations surrounding work equipment, competency requirements for maintenance and installation contractors, competency requirements for users of work equipment, required maintenance intervals, and the completion of routine internal inspections.
The Importance of Safe Work Equipment
Moral obligations
It’s important that we as employers look after our employees and anyone affected by any work we do. Employees who face poorly controlled risks to their health and wellbeing at work are unlikely to work to their full capacity and will feel undervalued.
Legal obligations
Statutory obligations and breaking the law could result in a court case, compensation, negligence claim (both civil & criminal law).
Financial obligations
- Loss of time (time to investigate and time liaising with legal department & insurers)
- Agency staff cover
- Replacement of equipment
- Compensation claims
- Legal fees
- HSE Fees for Intervention
Reputational Damage
If things go wrong, having poor health and safety management can detrimentally impact the school or Trust’s reputation. Situations such as injuries, fatalities or fires can severely impact both the community and the perception of the school or trust.
The Regulations Surrounding Work Equipment
Health and Safety at Work Act
This legislation covers occupational health and safety in Great Britain. It's sometimes referred to as HSWA, the HSW Act, the 1974 Act or HASAWA.
It sets out the general duties which:- employers have towards employees and members of the public.
- employees have to themselves and to each other.
- certain self-employed have towards themselves and others.
Provision and Use of Work Equipment Regulations 1998 (PUWER)
These are the primary Regulations, often abbreviated to PUWER, which place duties on people and companies who own, operate or have control over work equipment. PUWER also places responsibilities on businesses and organisations whose employees use work equipment, whether owned by them or not.
The basic 5 PUWER requirements for work equipment are:- Suitable for the intended use.
- Safe for use, maintained in a safe condition and inspected to ensure it is correctly installed and does not subsequently deteriorate.
- Used only by people who have received adequate information, instruction and training.
- Accompanied by suitable health and safety measures, such as protective devices and controls. These will normally include guarding, emergency stop devices, adequate means of isolation from sources of energy, clearly visible markings and warning devices.
- Used in accordance with specific requirements, for mobile work equipment and power presses.
NB: You must consider the particular risks associated with the individual pieces of equipment. For example, some equipment might require a guard, safety markings, PPE, etc.
Management of Health and Safety at Work Regulations 1999
These regulations outline what employers, managers and other duty holders are required to do to manage health and safety. They apply to every work activity. The regulations place a set of duties on employers and employees to maintain a safe and healthy workplace.
Lifting Operations and Lifting Equipment Regulations 1998 (LOLER)
If your school or trust undertakes lifting operations or is involved in providing lifting equipment for others to use, you must manage and control the risks to avoid any injury or damage.
LOLER requires all equipment used for lifting is:- fit for purpose.
- appropriate for the task.
- suitably marked.
- subject to statutory periodic 'thorough examination'.
Records must be kept of all thorough examinations and any defects found must be reported to both the person responsible for the equipment and the relevant enforcing authority.
Safe use of lifting equipment: Approved Code of Practice (ACOP)
While the ACOP is not law, it has a special status. It supports LOLER along with the general provisions of section 2 of the HSW Act and other regulations, including the Management of Health and Safety at Work Regulations and PUWER overview, in relation to lifting equipment and lifting operations.
New Equipment
When ordering work equipment, it is important to maintain due diligence. Often staff members may request certain equipment that may not be compliant.
Once you have obtained a new piece of equipment from a reputable supplier, you should check the manufacturer’s guidelines, know the inspection regime for it, and assess training requirements for all users.
Documentation
You should have risk assessments for the equipment, manufacturer’s guidance, inspection/servicing/maintenance records, guidelines for use such as a ‘safe system of work’ instruction sheet, training records, and a list of authorised users.
The Competency Requirements for Maintenance and Installation Contractors
It is incredibly important schools and trusts use competent contractors and vet competency. We recommend you have a Competent Contractors Policy which includes all your procedures to manage contractors.
Criteria for assessing contractor competency:- Relevant qualifications and certifications.
- Risk assessments, method statements and insurance.
- Experience and expertise.
- Compliance with health and safety standards.
- Obtaining and verifying references.
NB: Sending a questionnaire requesting the above information to all potential contractors is a good starting point.
Competency Requirements for Users of Work Equipment
Responsibilities of users include:- Understanding equipment operation and hazards
- Following manufacturer's instructions and safety guidelines
- Reporting defects and concerns promptly
- Importance of ongoing training and refresher courses
NB: Training levels should be relevant to the type of equipment and meet guidance.
Maintenance, Servicing & Testing Intervals
The primary factors influencing maintenance intervals are:
- Frequency and intensity of equipment use.
- Manufacturer recommendations.
- Legal requirements and industry standards.
- Examples of common maintenance tasks and intervals include an annual external audit for most equipment. For heavy use equipment such as play equipment, etc internal bi-weekly or monthly inspections and records of these inspections are recommended.
Completion of Routine Internal Inspections
Who should conduct internal inspections:
- Trained staff members
- Designated competent persons
Key inspection procedures:
- Visual checks for wear, damage, and defects
- Functional tests to ensure proper operation
- Documentation of findings and actions taken
Key takeaways
- Know what you’ve got. Assess what equipment you have at your site.
- Develop a scheme of inspection which considers the legal requirements and best practice recommendations.
- Internal staff must be trained appropriately.
- Make sure you are using competent contractors.
- Ensure you have all your documentation in place.
- Use the right tool for the right job.
Additional Information
The Health and Safety Service is also providing accredited training courses, including eLearning with specific modules ranging from courses designed for premises managers and SLT to all staff offerings and fire warden training: https://www.judiciumeducation.co.uk/elearning
We also offer live, exclusive training options: https://www.judiciumeducation.co.uk/training
To review Judicium’s forthcoming sofa sessions please click here.
Follow us on Twitter - @JudiciumEDU
© This content is the exclusive property of Judicium Education. The works are intended to provide an overview of the sofa session you attend and/or to be a learning aid to assist you and your school. However, any redistribution or reproduction of part or all of the contents in any form is prohibited. You may not, except with our express written permission, distribute or exploit the content. Failure to follow this guidance may result in Judicium either preventing you with access to our sessions and/or follow up content.
Related content
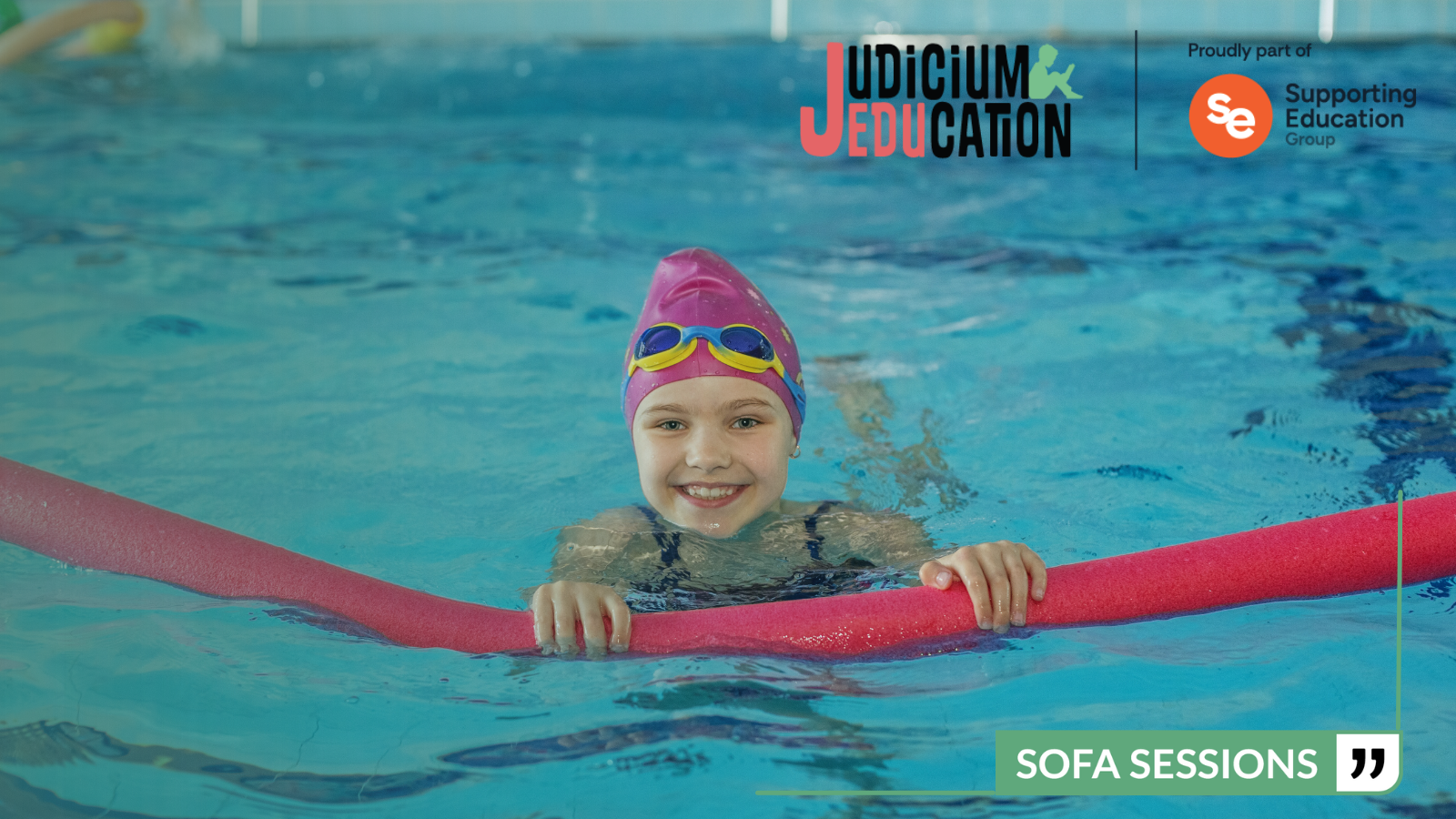
This blog is based on Judicium’s Health and Safety ‘Sofa Session’ from the 2nd of July, with our resident expert Jonathan Friend and India Cottenden.
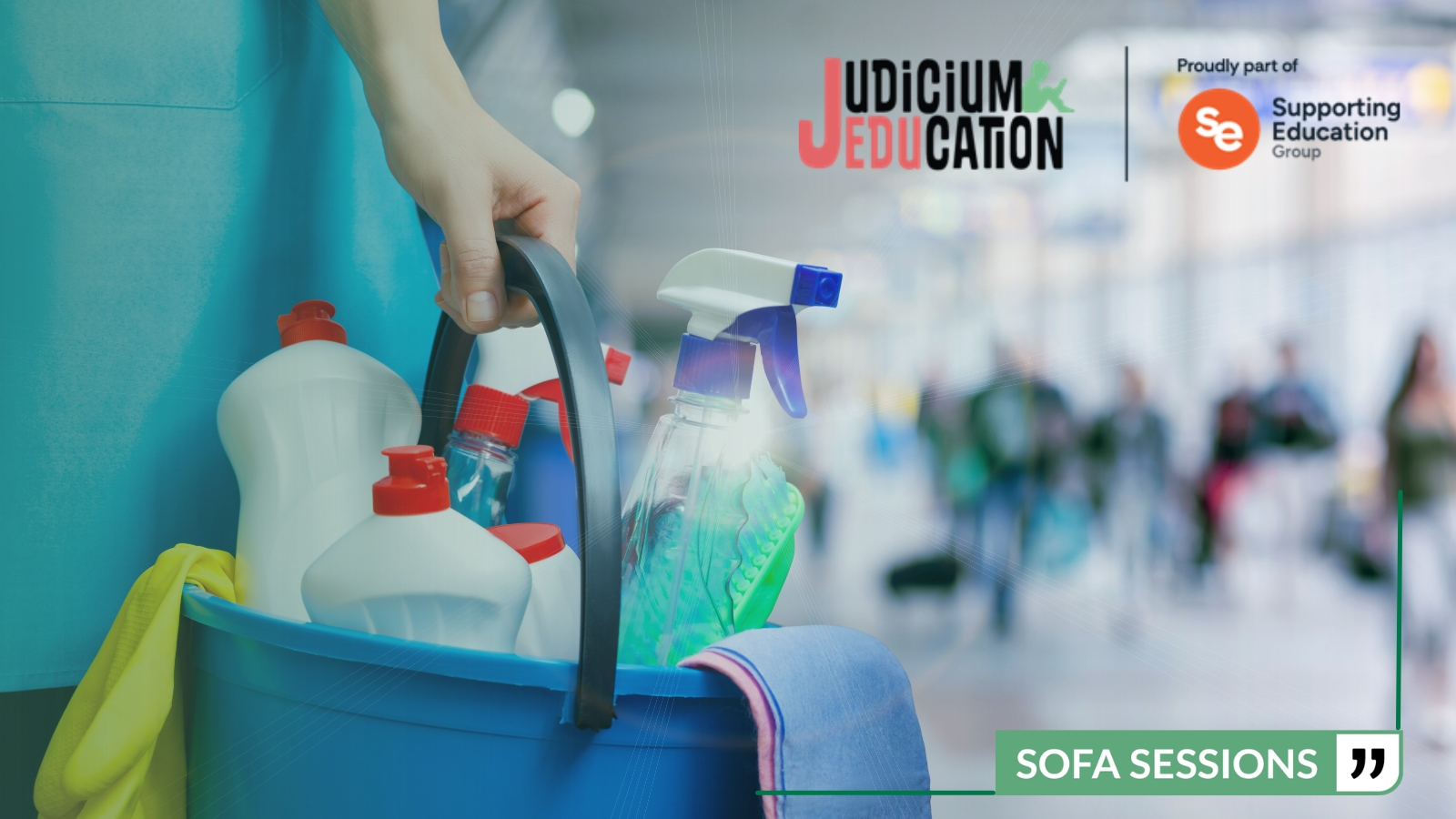
This blog is based on Judicium’s Health and Safety ‘Sofa Session’ from 18th June, led by resident expert , Mike Wright, CMIOSH. This session focuses on the control of substances hazardous to health (COSHH) and their relevance in school settings, how assessments should be undertaken and what staff could be at risk.
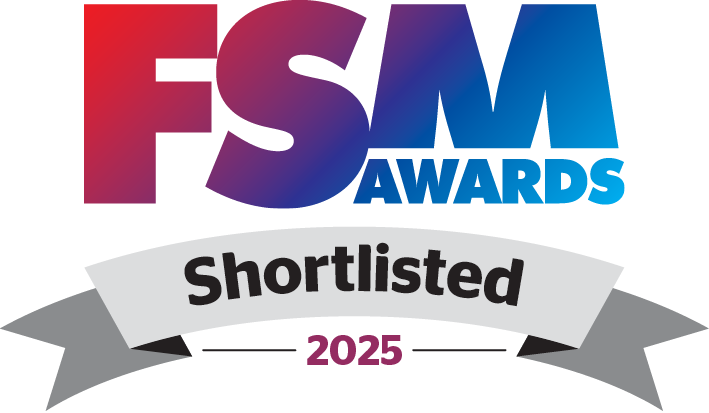
Discover why Judicium has been shortlisted for Fire Safety Consultancy of the Year at the 2025 FSM Awards, recognising our expert support for schools and trusts in delivering sector-specific, compliant, and practical fire safety solutions.
.png)
This blog is based on Judicium’s Health and Safety ‘Sofa Session’ from the 12th of March, with our resident expert Mike Wright.
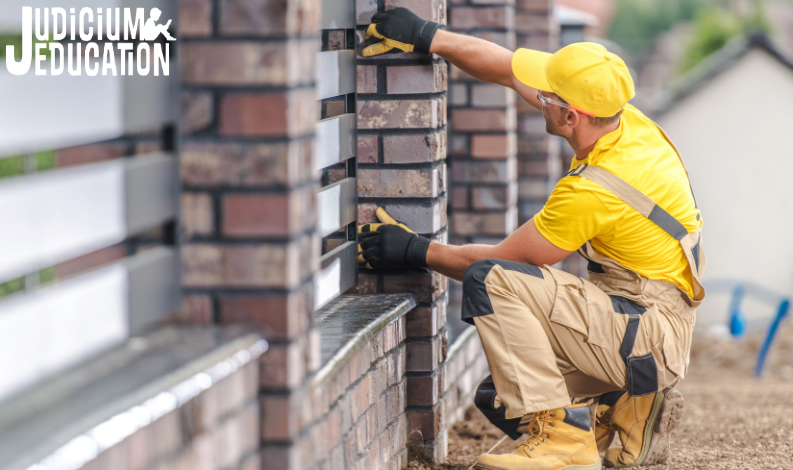
This blog is based on Judicium’s Health and Safety ‘Sofa Session’ from the 26th of February, with our resident expert Loretta Igbe.
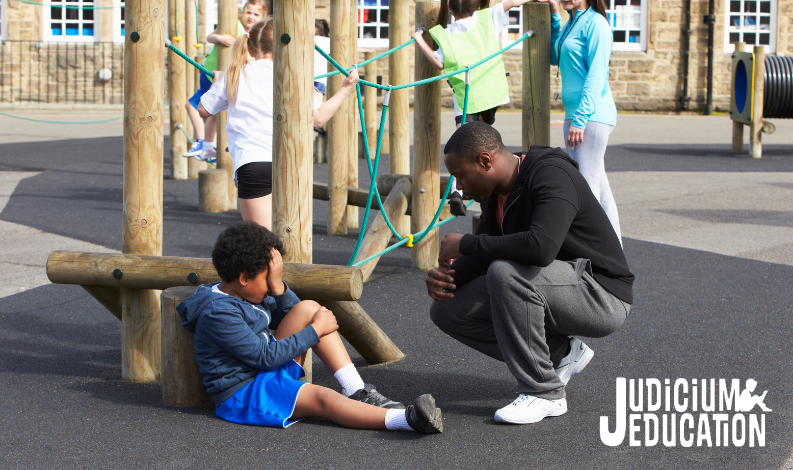
This blog is based on Judicium’s Health and Safety ‘Sofa Session’ from the 8th of January, with our resident expert Jim Liddy.
Sofa Sessions | H&S